Introduction
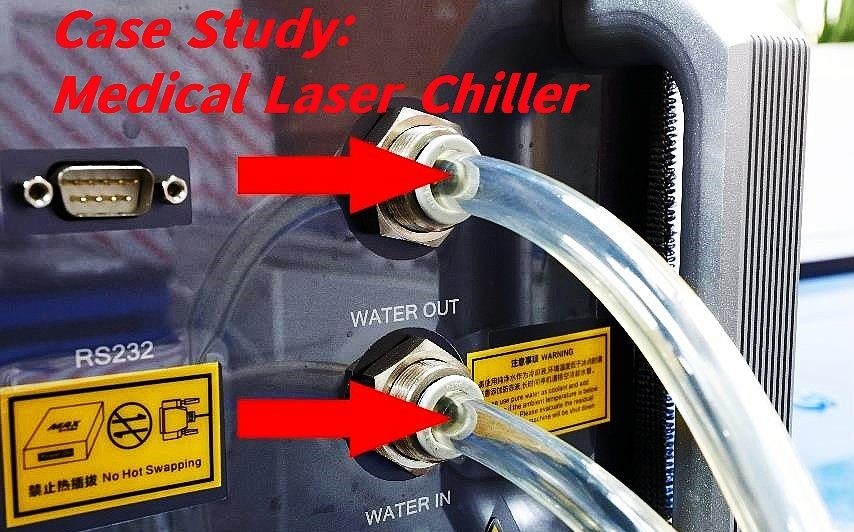
"Arctic Active Cooling. Endless Possibilities. We capture new technologies in mobile and compact cooling. Full-size cooling in a miniature design, customized to make your device stand out with innovative thermal management."
In the world of laser cutting, maintaining optimal operating conditions is crucial for achieving high-quality results and prolonging the lifespan of your equipment. This is where the importance of keeping cool comes into play; excessive heat can wreak havoc on your laser cutter's performance and efficiency. Enter the water chiller for laser cutter—your trusty sidekick in managing heat generation and ensuring smooth operations.
The Importance of Keeping Cool
Keeping cool isn't just a catchy phrase; it's a necessity when it comes to laser cutting. Heat buildup can lead to a myriad of problems, including reduced precision, compromised material integrity, and even costly equipment damage. By investing in a reliable water chiller for laser cutter setups, you can safeguard your investment while enhancing overall performance.
Laser Cutters and Heat Generation
Laser cutters generate significant heat during operation due to their high-powered beams interacting with materials. This heat not only affects the quality of cuts but also poses risks such as overheating components or causing malfunctions. Understanding how to manage this heat effectively raises an essential question: Do I need a water chiller for my laser? The answer often lies in recognizing the signs that indicate it's time to integrate cooling solutions into your setup.
What is a Water Chiller?
A water chiller is a specialized cooling system designed to regulate temperatures in various applications, including laser cutting machines. These systems circulate chilled water through critical components, absorbing excess heat and maintaining optimal operating temperatures. With questions like What temperature should a laser cutter chiller be? frequently arising among users, understanding these systems becomes vital for anyone serious about maintaining their equipment's efficiency.
Understanding Water Chill Technology
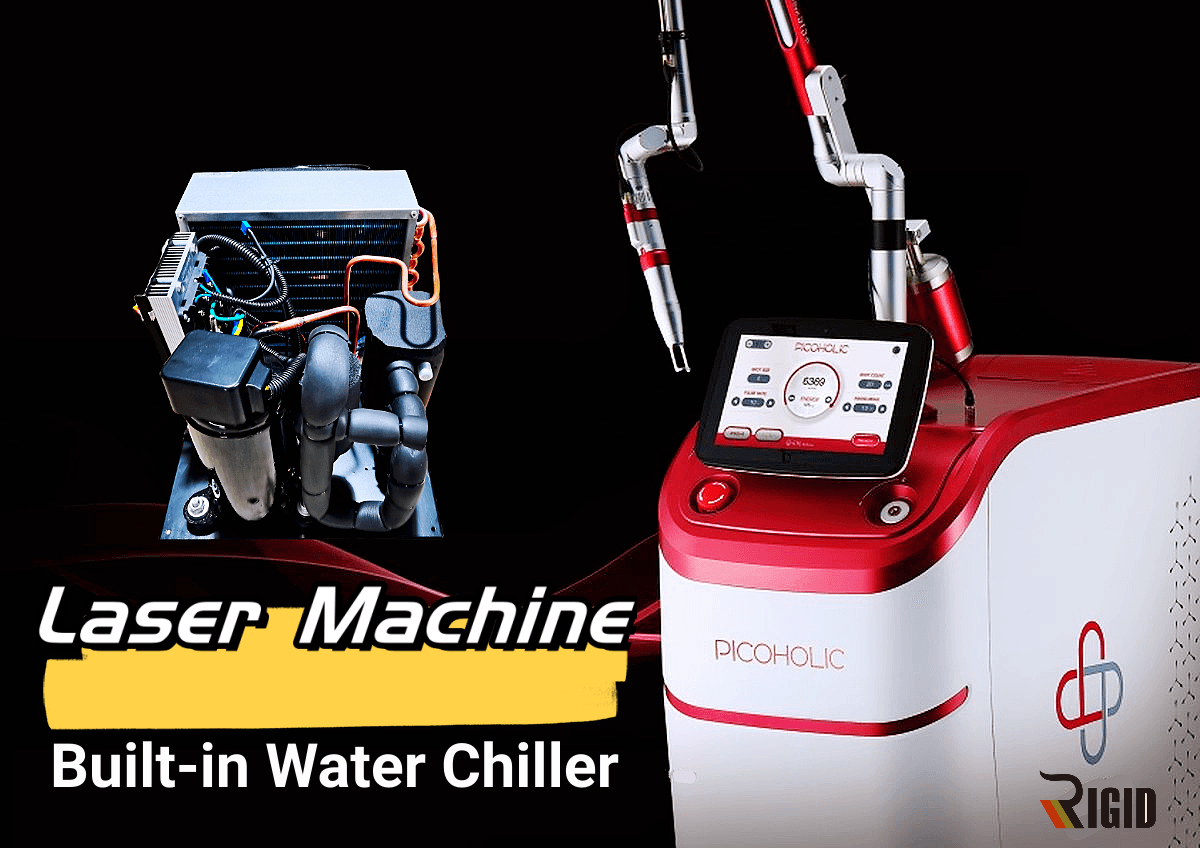
Water chillers play a crucial role in maintaining the efficiency and longevity of laser cutting machines. By regulating temperature, they prevent overheating, ensuring consistent performance and high-quality cuts. Understanding how these systems work can help you decide if you need a water chiller for your laser cutter.
How a Water Chiller Works
A water chiller operates by circulating coolant through the laser cutter's components to absorb excess heat generated during operation. This coolant is then cooled down in the chiller unit before being recirculated back to the machine, creating a continuous cycle of cooling. Essentially, it’s like giving your laser cutter a refreshing drink on a hot day—keeping it cool and functioning smoothly.
Benefits of Using Water Chillers
Using a water chiller for your laser cutter comes with numerous benefits that can enhance both performance and safety. First off, they significantly reduce the risk of overheating, which can lead to equipment failure or reduced cutting quality—definitely not something you want on your watch! Additionally, maintaining optimal temperatures can improve cutting precision and extend the life of your machine; after all, nobody wants to replace their equipment prematurely.
The Role of Chillers in Laser Cutting
The purpose of chillers in laser cutting machines cannot be overstated; they are essential for ensuring that everything runs like a well-oiled machine (or should we say well-cooled?). By keeping components at stable temperatures, chillers help maintain consistent power output from the laser, which is vital for achieving clean cuts every time. Plus, when you consider factors like speed and quality in production environments, investing in one of the best water cooling systems becomes an obvious choice for any serious operator.
Do I Need a Water Chiller for My Laser?
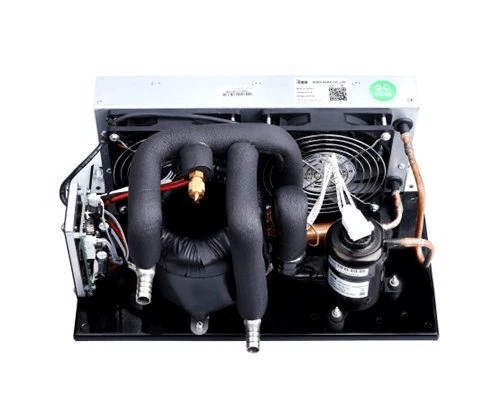
Signs Your Laser Cutter Needs Cooling
There are several telltale signs indicating that your laser cutter may need cooling assistance from a water chiller. If you notice inconsistent cutting quality or your machine frequently shuts down due to overheating, it's time to consider investing in a reliable cooling system. Additionally, if the components of your laser cutter feel excessively hot to the touch after prolonged use, that’s a clear sign that it could benefit from enhanced cooling solutions.
Risks of Operating Without a Chiller
Operating without an adequate water chiller for your laser cutter can lead to serious risks and complications. Overheating can cause damage not only to the laser tube but also to other critical components like optics and electronics, potentially leading to costly repairs or replacements. Moreover, excessive heat can impact cutting precision and quality, resulting in subpar results that could affect your business's reputation.
Enhancing Performance with a Chiller
Investing in a water chiller enhances performance significantly by maintaining consistent temperatures during operation. This consistency ensures that your cuts remain precise and clean across various materials while reducing downtime caused by overheating issues. Ultimately, using the best water cooling systems allows you to maximize productivity and extend the lifespan of your equipment while safeguarding against potential failures.
What Temperature Should a Laser Cutter Chiller Be?
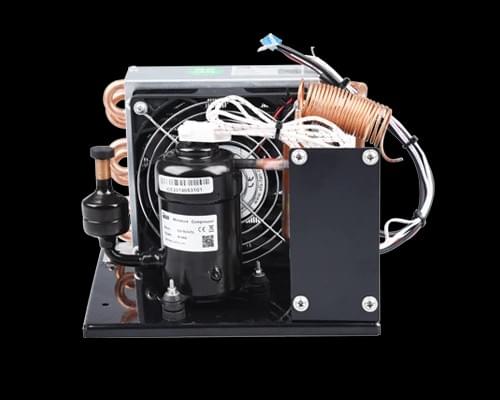
Maintaining the right temperature for your water chiller for laser cutter is crucial for optimal performance and longevity of your equipment. A well-functioning chiller not only keeps the laser cutting components cool but also ensures that you achieve high-quality cuts consistently. So, what temperature should a laser cutter chiller be set at to strike that perfect balance between efficiency and safety?
Ideal Temperature Ranges
Generally, the ideal temperature range for a water chiller in laser cutting applications falls between 18°C to 22°C (64°F to 72°F). This range helps prevent overheating while ensuring that your laser cutter operates smoothly without any hiccups. If you're wondering, Do I need a water chiller for my laser?, the answer is yes—especially if you want to maintain this optimal temperature.
Effects of Temperature on Cutting Quality
Temperature fluctuations can significantly impact cutting quality, with warmer temperatures often leading to reduced precision and increased wear on components. When the water chiller operates outside its ideal range, you may experience issues like inconsistent cuts or even damage to materials being processed. Therefore, understanding What is the purpose of a chiller in a laser cutting machine? becomes clear: it maintains stable temperatures essential for achieving desired results.
Tips for Maintaining Optimal Temperature
To keep your water chiller functioning at its best, regularly check and adjust its settings based on ambient conditions and usage levels. Consider investing in high-quality monitoring systems that alert you when temperatures deviate from their ideal ranges; this proactive approach can save you headaches later on! Additionally, routine maintenance of both your water chiller and laser cutter will ensure they work harmoniously together—because nobody wants to ask themselves What size water chiller do I need? after facing performance issues due to neglect.
What is the Purpose of a Chiller in Laser Cutting Machine?
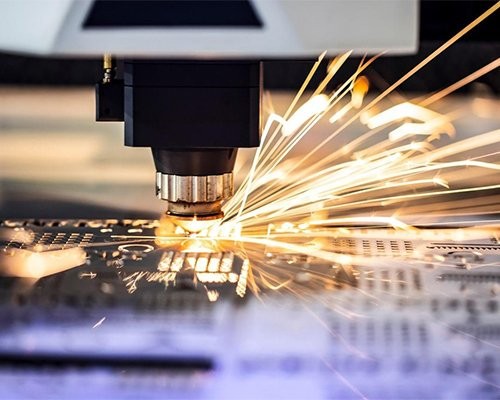
When it comes to laser cutting machines, understanding the purpose of a water chiller is crucial for optimal performance. A water chiller for laser cutter systems plays a vital role in ensuring that the machine operates efficiently and effectively. By managing heat generation, these chillers help maintain peak performance, which is essential for high-quality cuts and prolonged equipment life.
Cooling Components to Prevent Overheating
One primary function of a chiller in laser cutting machines is cooling components to prevent overheating. High temperatures can lead to thermal stress on various parts, potentially causing malfunctions or even permanent damage. By utilizing a water chiller for laser cutter applications, you can keep temperatures within safe limits, thus avoiding costly repairs and downtime.
Overheating not only affects the machine but also compromises the quality of your work. If you find yourself asking, Do I need a water chiller for my laser? consider how often your machine runs at high power settings; if it's frequent, then cooling becomes imperative. Keeping your equipment cool ensures that it runs smoothly and maintains its efficiency over time.
Maintaining Consistent Laser Performance
Another critical purpose of a chiller in laser cutting machines is maintaining consistent laser performance throughout operations. Fluctuations in temperature can lead to variations in cutting quality—something no one wants when precision is key! A water chiller helps stabilize the temperature around the laser tube and other sensitive components, ensuring that each cut meets your expectations.
When you're working with materials that require precise cuts or engravings, maintaining consistent performance becomes even more essential. If you’re wondering what temperature should a laser cutter chiller be set at, remember that optimal cooling directly influences how well your machine performs during those intricate tasks. Consistency leads not just to better outcomes but also enhances overall productivity.
Enhancing Longevity of Equipment
The last piece of the puzzle regarding what is the purpose of a chiller in laser cutting machines lies in enhancing equipment longevity. Regularly operating at elevated temperatures can significantly reduce the lifespan of key components like lasers and motors—no one wants their investment to fizzle out prematurely! With an effective water chiller for laser cutter systems in place, you can extend operational life by mitigating wear and tear caused by excessive heat.
Additionally, users often overlook maintenance practices when considering how long their equipment will last; however, having a reliable cooling system makes upkeep easier and more effective. You might be thinking about what size water chiller do I need? The right size will ensure efficient operation while prolonging your machine's lifespan through effective thermal management strategies.
In conclusion, investing in one of the best water cooling systems available will pay off not just today but down the line as well—ensuring that your projects are completed with precision while keeping your equipment running smoothly for years to come!
What Size Water Chiller Do I Need?
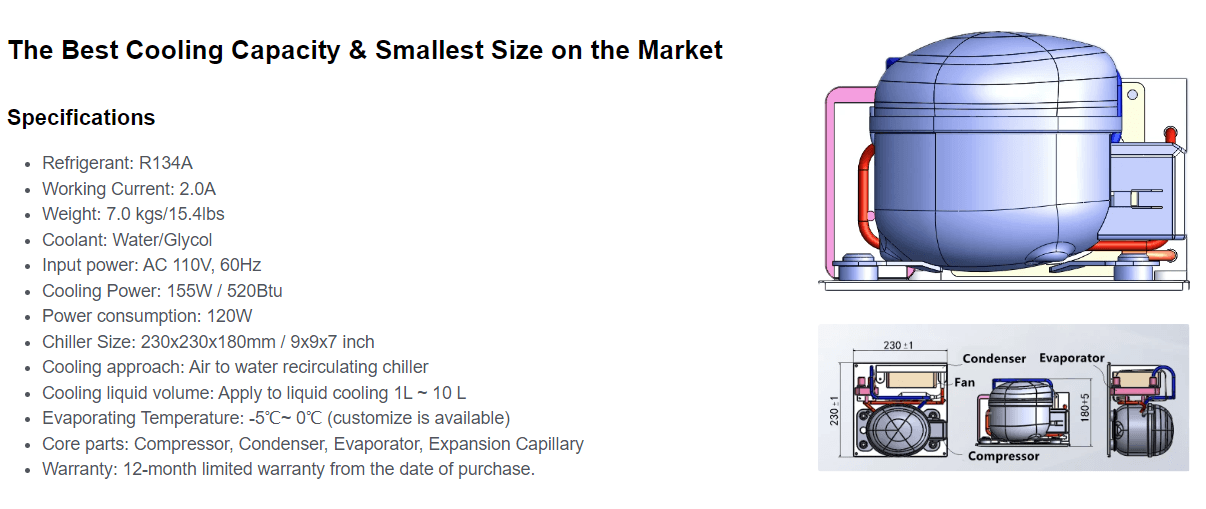
Factors to Consider When Sizing
The first step in determining the appropriate size for a water chiller is understanding your laser cutter's cooling requirements. Factors such as wattage, operational hours, and the environment where the machine operates play crucial roles in this decision-making process. Additionally, consider whether you’re using your laser cutter for light-duty work or heavy industrial applications; heavier usage typically demands more robust cooling solutions.
Another important aspect is the ambient temperature of your workspace. If you're operating in a hot environment, you may need a more powerful unit to maintain optimal temperatures efficiently. Lastly, don’t forget about future scalability; if you plan on upgrading or expanding your operations down the line, it's wise to choose a chiller that can accommodate increased demands.
Common Sizes and Their Applications
Water chillers come in various sizes tailored for different applications—ranging from small units suitable for hobbyist setups to larger systems designed for industrial-grade machines. For instance, compact chillers with capacities around 1/4 HP are often sufficient for smaller laser cutters used in home workshops or small businesses. Meanwhile, medium-sized chillers (1/2 HP to 1 HP) are popular choices among mid-sized operations needing consistent cooling without breaking the bank.
For heavy-duty industrial applications that run continuously at high wattages, you'll likely need chillers rated above 1 HP—sometimes even up to 5 HP or more! These units ensure that high-performance lasers maintain their cutting quality without overheating during extended use. When asking yourself Do I need a water chiller for my laser?, remember that selecting the right size can make all the difference!
How ARCTIC Chillers Meet Your Needs
ARCTIC Chillers offer an impressive range of options tailored specifically for laser cutting machines. With models designed to suit various sizes and specifications, they provide reliable cooling solutions that enhance performance and extend equipment longevity. Their efficient designs not only keep temperatures within ideal ranges but also optimize energy consumption—making them one of the best water cooling systems available on the market.
Moreover, ARCTIC's commitment to quality means their chillers are built with durable components designed to withstand demanding environments while maintaining consistent performance over time. This reliability ensures you're not just investing in a product but also peace of mind knowing you're equipped with one of the best options out there when it comes time to ask What temperature should a laser cutter chiller be?
In conclusion, selecting an appropriately sized water chiller is essential for ensuring optimal operation of your laser cutting machine while preventing overheating issues associated with poor thermal management.
Conclusion
In the world of laser cutting, maintaining optimal temperatures is not just a luxury; it’s a necessity. A quality water chiller for laser cutter systems can be the difference between a smooth operation and costly downtime due to overheating. With the right cooling system in place, you can ensure that your equipment runs efficiently and lasts longer.
The Case for Quality Water Cooling Systems
When considering whether you need a water chiller for your laser cutter, remember that quality matters. High-performance chillers are designed to handle the heat generated by laser cutting processes effectively, ensuring consistent performance and preventing damage to sensitive components. Investing in the best water cooling systems will pay dividends in terms of reliability, efficiency, and overall output quality.
Choosing the Right Chiller for You
Selecting the right size water chiller is crucial; too small and it won’t cool effectively, too large and it may be overkill for your needs. Factors such as your laser cutter's wattage, work environment, and specific applications will guide you in making an informed decision. Remember to ask yourself: Do I need a water chiller for my laser? If you're serious about preserving your equipment's lifespan and enhancing performance, then the answer is likely yes.
Final Thoughts on Keeping Your Laser Cutter Efficient
Ultimately, understanding what temperature should a laser cutter chiller be set at can help maintain optimal cutting conditions while minimizing wear on your machine. Regular maintenance of your cooling system ensures that it operates efficiently over time—after all, nobody wants to deal with unexpected breakdowns! So equip yourself with knowledge about what is the purpose of a chiller in laser cutting machine operations and choose wisely when selecting what size water chiller do I need for my setup.