Introduction
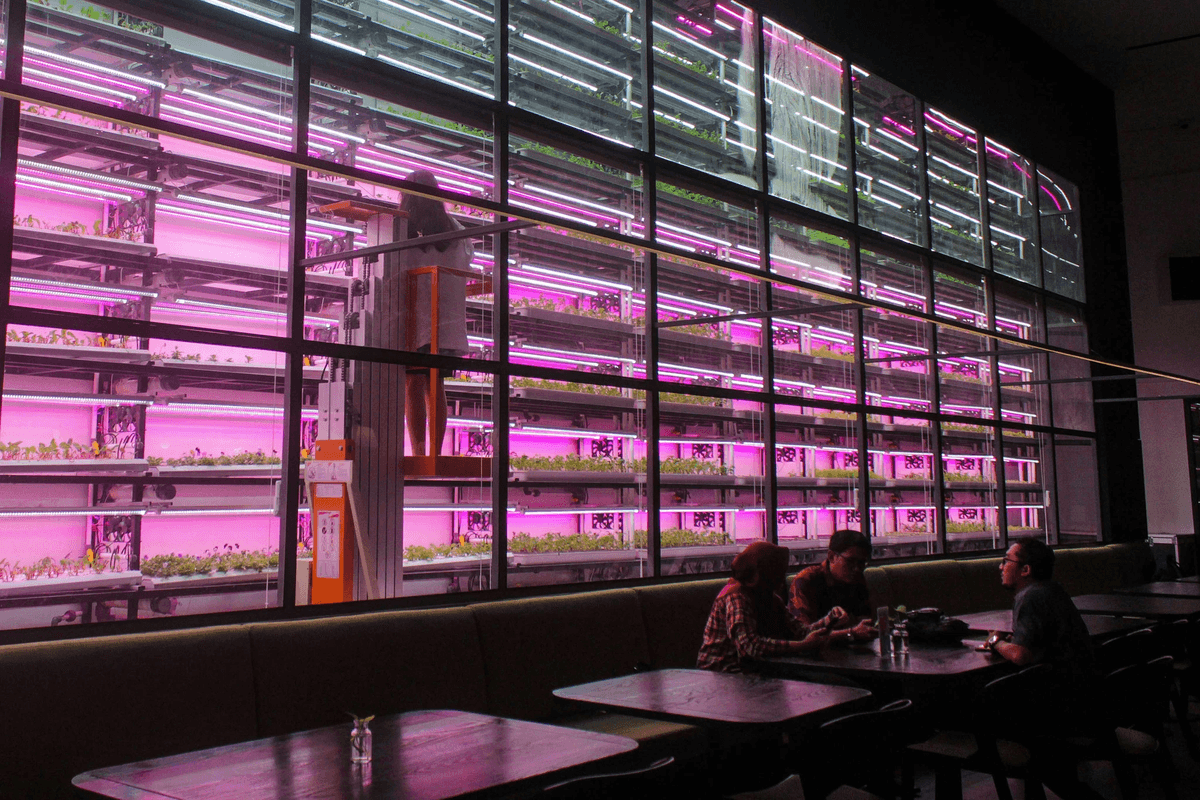
"Arctic Active Cooling. Endless Possibilities. We capture new technologies in mobile and compact cooling. Full-size cooling in a miniature design, customized to make your device stand out with innovative thermal management."
Industrial chillers are essential components in various industries, providing efficient cooling solutions for processes that require temperature control. But what are industrial chillers? In essence, they are specialized refrigeration systems designed to remove heat from a fluid through a vapor-compression or absorption refrigeration cycle. Understanding the mechanics behind these systems is crucial for optimizing performance and ensuring longevity.
Understanding Industrial Chillers
When diving into the world of industrial chillers, it's important to grasp their primary function: cooling fluids that circulate through machinery or equipment. This process is vital in industries such as food and beverage, chemical manufacturing, and data centers where precise temperature management is critical. So, what are the three types of chillers? Generally, they can be categorized into air-cooled, water-cooled, and absorption chillers—each serving unique applications based on efficiency needs and environmental conditions.
Importance of Efficiency in Cooling
Efficiency in cooling is not just a buzzword; it’s a necessity for reducing operational costs and minimizing environmental impact. With rising energy prices and increasing regulatory pressures, businesses must prioritize efficient industrial chillers to stay competitive. The choice between different types of industrial chillers can significantly affect both energy consumption and overall system performance.
Key Components of Chiller Systems
Every chiller system comprises several key components that work together to ensure effective cooling operations. These include compressors, condensers, evaporators, expansion valves, and heat exchangers—each playing a pivotal role in the refrigeration cycle. Understanding these components allows users to better appreciate how industrial chillers function as part of larger HVAC systems while also facilitating informed decisions when selecting from various industrial chillers manufacturers or exploring options for industrial chillers for sale.
Types of Industrial Chillers
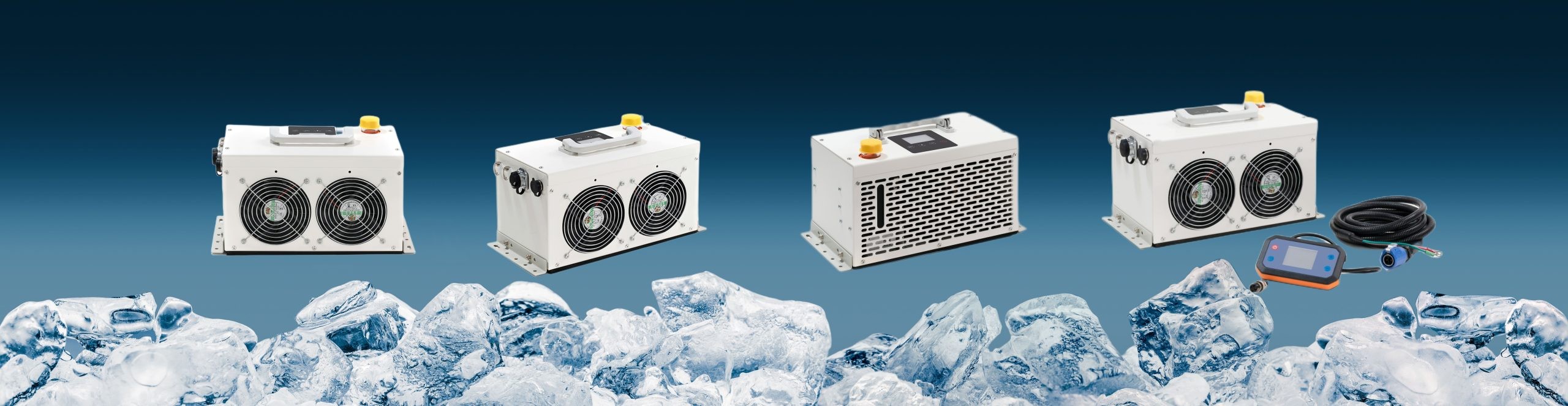
Air-Cooled vs. Water-Cooled Chillers
Air-cooled and water-cooled chillers represent two primary categories of industrial chillers that cater to different operational requirements. Air-cooled chillers use ambient air to dissipate heat, making them ideal for installations where water availability is limited or where maintenance concerns arise. On the other hand, water-cooled chillers utilize water from a cooling tower or another source for heat exchange, often providing higher efficiency and better performance in larger applications.
The choice between air-cooled and water-cooled systems can significantly impact operational costs and energy consumption. For instance, while air-cooled units may have lower upfront costs, their efficiency can decline during high-temperature conditions compared to their water-cooled counterparts. Understanding these differences helps businesses make informed decisions about which type of chiller best suits their needs.
Absorption Chillers Explained
Absorption chillers offer an alternative cooling solution by using heat instead of electricity to drive the refrigeration cycle. This makes them particularly appealing in situations where waste heat is available from industrial processes or cogeneration systems—essentially recycling energy that would otherwise be lost. So when considering what are the three types of chillers? Absorption chillers certainly make the list alongside air-cooled and water-cooled options.
These systems operate on principles similar to traditional vapor-compression units but utilize refrigerants like lithium bromide or ammonia instead of mechanical compressors. As a result, absorption chillers can provide significant energy savings when integrated into existing heating systems or renewable energy sources. However, they often come with a higher initial investment and might not be suitable for every application.
Arctic Active Cooling DC Condensing Unit
The Arctic Active Cooling DC condensing unit is a cutting-edge innovation in the realm of industrial chillers designed for maximum efficiency and flexibility in cooling applications. Utilizing direct current technology allows these units to operate more quietly while consuming less energy than traditional AC models—an attractive feature for industries looking to reduce operational costs while maintaining high-performance standards.
Manufacturers producing such advanced solutions include some well-known names within the industry who specialize in creating tailored options based on specific client requirements—so it's worth exploring who makes industrial chillers if you're considering an upgrade or new installation! With prices varying widely depending on specifications and features offered by different manufacturers, it's essential to compare options before making a purchase decision.
In summary, understanding various types of industrial chillers—including air-cooled versus water-cooled models, absorption technologies, and innovative solutions like Arctic Active Cooling units—can empower businesses to optimize their cooling strategies effectively while keeping an eye on cost-efficiency as well as environmental impact.
How Industrial Chillers Work
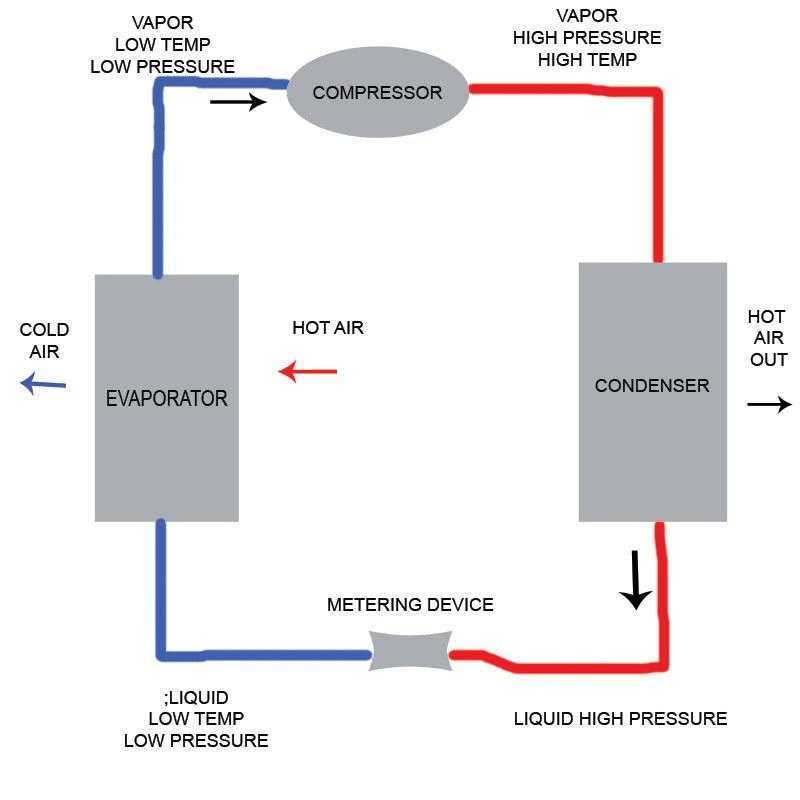
Understanding how industrial chillers work is crucial for anyone seeking to optimize their cooling systems. At the heart of this process are refrigerants, which play a pivotal role in transferring heat away from the areas that need cooling. This section will delve into the intricacies of these components, shedding light on their importance in industrial applications.
The Role of Refrigerants
Refrigerants are the lifeblood of any chiller system, responsible for absorbing and releasing heat during the cooling cycle. These substances undergo phase changes—from liquid to gas and back again—allowing them to effectively transfer heat away from industrial processes or spaces. When asking What are industrial chillers? it’s essential to recognize that without suitable refrigerants, these systems wouldn't be able to function efficiently or effectively.
Different types of chillers utilize various refrigerants based on factors like efficiency, environmental impact, and regulatory standards. For instance, some modern industrial chillers have shifted towards more eco-friendly options due to environmental concerns surrounding traditional refrigerants. Understanding who makes industrial chillers can also lead you to manufacturers that prioritize sustainable practices in their refrigerant choices.
Heat Absorption Process
The heat absorption process is where the magic happens in an industrial chiller system. As warm air passes over evaporator coils filled with low-pressure refrigerant, the refrigerant absorbs heat and evaporates into a gas—a crucial step in maintaining cool temperatures. This process not only helps answer What is a chiller vs HVAC? but also highlights how specialized equipment like industrial chillers operates differently compared to standard HVAC systems.
Once the refrigerant has absorbed enough heat, it moves on to the compressor, where it’s pressurized and heated further before entering the condenser coils. Here, it releases its absorbed heat as it condenses back into a liquid state—ready to start the cycle anew! Knowing how this cycle functions can greatly assist businesses when looking for industrial chillers for sale that meet their specific cooling needs.
Importance of Heat Exchangers
Heat exchangers are critical components within industrial chillers that facilitate efficient thermal energy transfer between fluids without mixing them together. They enhance overall system performance by maximizing surface area contact between hot and cold fluids while minimizing energy loss during this exchange process. For those interested in industrial chillers manufacturers, understanding how they incorporate advanced heat exchanger designs can be key when evaluating product options.
These devices come in various configurations—such as shell-and-tube or plate types—each designed for specific applications based on factors like space constraints and thermal load requirements. In essence, effective heat exchangers contribute significantly not only to operational efficiency but also influence overall industrial chillers price by impacting energy consumption levels over time.
In summary, grasping these fundamental processes behind how industrial chillers work will empower users to make informed decisions about maintenance and upgrades while promoting energy savings across operations.
Efficiency in Industrial Chillers
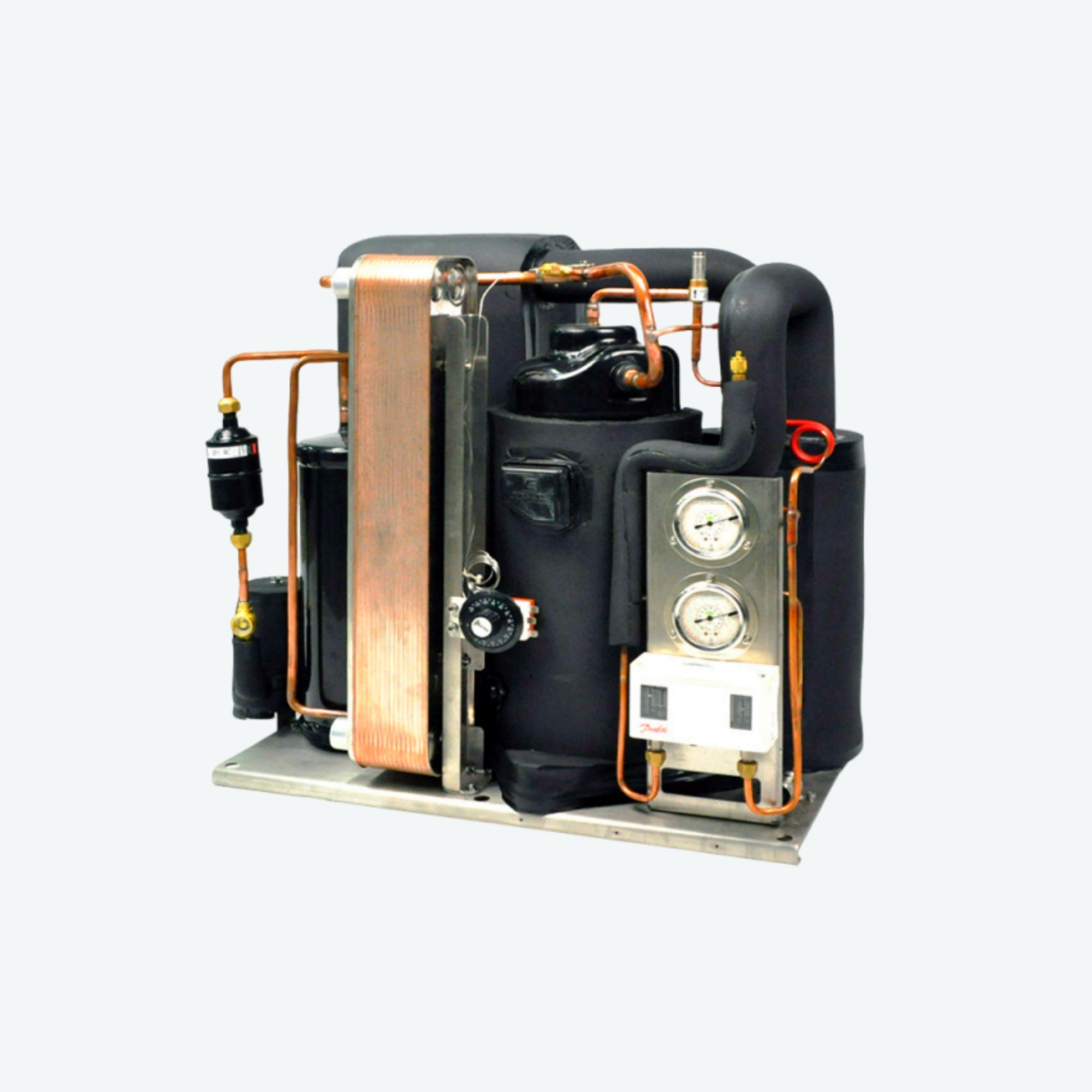
When it comes to industrial chillers, efficiency isn't just a buzzword—it's the lifeblood of operating costs and environmental impact. Understanding how to measure and enhance this efficiency is crucial for anyone involved in the cooling industry. Let's dive into some key metrics, maintenance practices, and smart choices that can lead to significant energy savings.
Key Efficiency Metrics
To evaluate the performance of industrial chillers, several key efficiency metrics come into play. The Coefficient of Performance (COP) is a primary metric that indicates how effectively a chiller converts electrical energy into cooling output; higher COP values signify better efficiency. Another important metric is the Energy Efficiency Ratio (EER), which measures cooling output per watt consumed; understanding these numbers can help you assess what are industrial chillers best suited for your needs.
Moreover, Seasonal Energy Efficiency Ratio (SEER) provides insights into chiller performance over an entire cooling season, making it easier to compare different models and manufacturers. When considering what are the three types of chillers—air-cooled, water-cooled, and absorption—their respective efficiencies will also depend on specific operational conditions and applications. Knowing these metrics allows businesses to make informed decisions when looking for industrial chillers for sale.
Impact of Maintenance on Performance
Regular maintenance is vital for maintaining optimal performance in industrial chillers; neglecting it can lead to decreased efficiency over time. Just like any complex machinery, components such as heat exchangers and refrigerants need periodic checks to ensure they’re functioning correctly; otherwise, you might find yourself asking what is a chiller vs HVAC when your system starts underperforming or breaking down altogether!
Furthermore, routine inspections can prevent costly repairs down the line by identifying potential issues before they escalate—a proactive approach often pays off in energy savings too! Industrial chillers manufacturers often recommend specific maintenance schedules tailored to their products; adhering to these guidelines can significantly extend the lifespan of your equipment while keeping operational costs low.
Choosing the Right Chiller for Energy Savings
Selecting the right industrial chiller involves more than just looking at price tags; it's about finding a balance between upfront costs and long-term savings on energy consumption. Factors like size, type (air-cooled or water-cooled), and intended application all play crucial roles in determining which model will yield maximum efficiency—after all, not all industrial chillers are created equal!
When considering who makes industrial chillers that fit your requirements best, look beyond just brand reputation; investigate their track record in energy-efficient technologies as well as customer reviews regarding long-term performance and reliability. By investing time upfront in research—considering options from various manufacturers—you'll be better positioned to choose an efficient solution that aligns with your budgetary constraints while delivering exceptional cooling capabilities.
Applications of Industrial Chillers

Industrial chillers play a crucial role in various sectors, ensuring processes remain efficient and products maintain quality. Their versatility allows them to be utilized in numerous applications, from food and beverage production to chemical manufacturing and data centers. Understanding these applications helps to highlight the importance of industrial chillers in modern industry.
Uses in Food and Beverage Industries
In the food and beverage industries, industrial chillers are indispensable for maintaining product quality and safety. They provide precise temperature control during processes such as fermentation, pasteurization, and cooling of finished products. With an array of industrial chillers for sale specifically designed for this sector, manufacturers can ensure compliance with health regulations while optimizing energy efficiency.
Food processing facilities often ask, What are industrial chillers? They need reliable systems that can handle fluctuations in demand without compromising performance. The right chiller not only enhances productivity but also contributes to lower operational costs—an attractive proposition for any food manufacturer.
Role in Chemical Manufacturing
Chemical manufacturing relies heavily on industrial chillers to manage exothermic reactions where heat removal is critical. These systems help regulate temperatures during production processes, preventing overheating that could lead to accidents or product degradation. By utilizing advanced industrial chillers from reputable manufacturers, companies can enhance their safety protocols while maximizing efficiency.
When considering What are the three types of chillers? many chemical plants opt for water-cooled or absorption chillers due to their effectiveness in high-demand environments. The choice between air-cooled or water-cooled systems often depends on specific operational needs and environmental conditions. Ultimately, selecting the right chiller is vital for maintaining consistent quality in chemical products.
Cooling Solutions for Data Centers
Data centers generate significant heat due to dense server configurations; thus, effective cooling solutions are essential to ensure optimal performance and reliability of IT equipment. Industrial chillers provide a robust solution by efficiently dissipating heat generated by servers and other electronic devices. Companies looking into Who makes industrial chillers? will find various options tailored specifically for data center applications.
As businesses increasingly rely on technology, understanding the distinction between a chiller vs HVAC becomes crucial; while both systems contribute to temperature control, their functions differ significantly within data centers. Properly selected industrial chillers not only enhance cooling efficiency but also contribute significantly to energy savings—an essential factor given rising energy costs today.
With the rapid growth of digital infrastructure, investing in high-quality industrial chillers has become a priority across industries aiming for sustainability without sacrificing performance.
Innovations in Chiller Technology
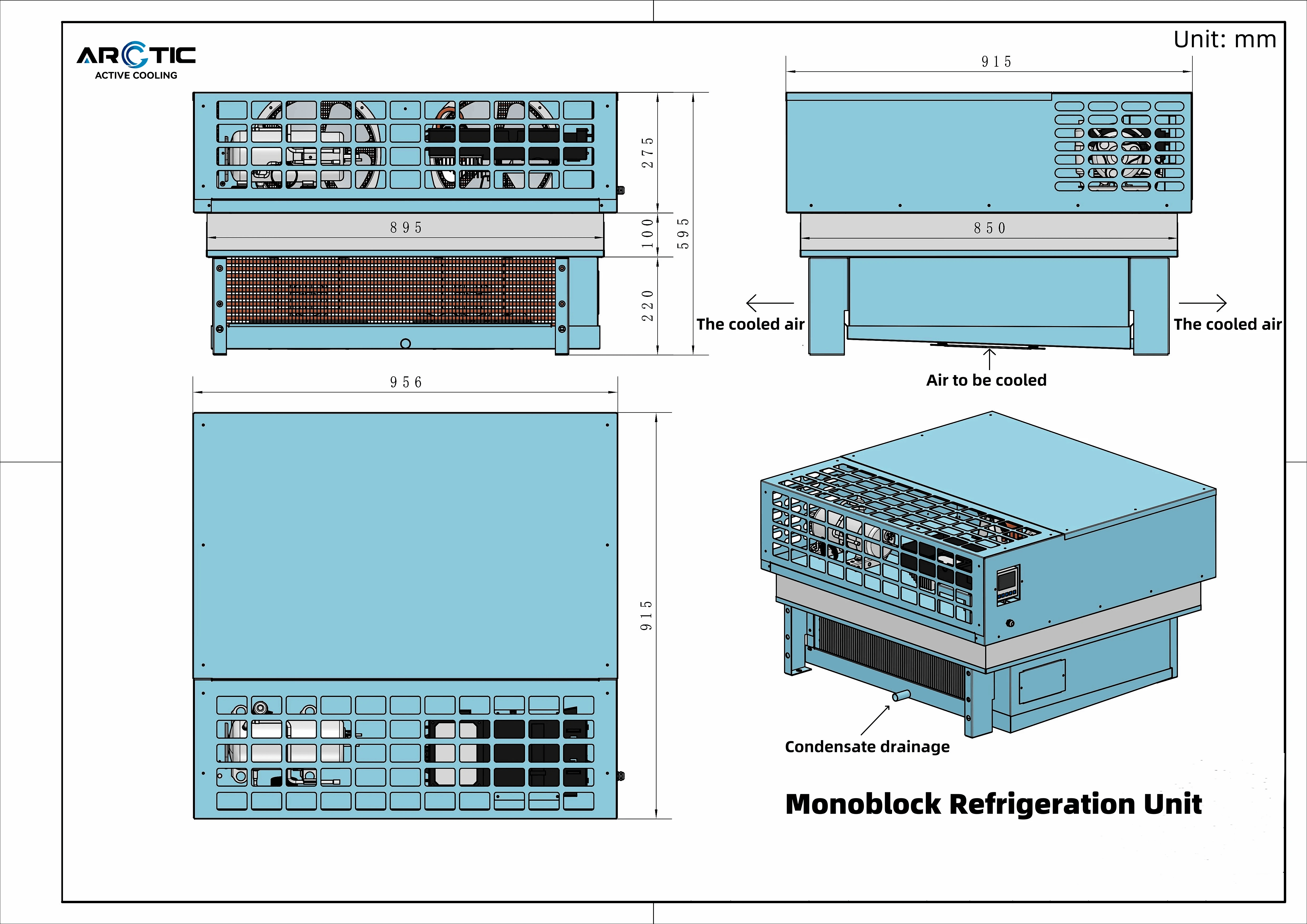
The world of industrial chillers is undergoing a fascinating transformation, driven by technological advancements and a growing emphasis on efficiency. As industries strive to reduce their carbon footprint and operational costs, innovations in chiller technology play a crucial role. From improved refrigerant options to smart automation systems, these developments are reshaping the landscape of cooling solutions.
Advances in Refrigerant Options
Refrigerants are at the heart of what makes industrial chillers effective, and recent advances have led to more environmentally friendly choices. Traditional refrigerants often contribute to ozone depletion and global warming, prompting manufacturers to explore alternatives that are less harmful. The latest options include low-GWP (Global Warming Potential) refrigerants that not only comply with environmental regulations but also enhance the efficiency of industrial chillers.
Many manufacturers are now focusing on developing blends that optimize performance while minimizing ecological impact. These advancements not only help industries meet compliance standards but also reduce energy consumption—an essential factor considering the rising industrial chillers price driven by energy costs. With companies like Daikin and Trane leading the charge, it's clear that the future of refrigerants is bright and green.
Smart Controls and Automation
The integration of smart controls and automation systems has revolutionized how industrial chillers operate. These technologies allow for real-time monitoring and adjustments based on varying load demands, ensuring optimal performance at all times. By implementing advanced algorithms, businesses can significantly enhance energy efficiency while reducing operational costs—an attractive proposition for those looking at industrial chillers for sale.
Moreover, smart controls enable predictive maintenance by analyzing data trends over time, which helps prevent costly breakdowns before they occur. This proactive approach is particularly beneficial for industries reliant on consistent cooling processes such as food production or chemical manufacturing. As more manufacturers embrace these innovations, it becomes clear that automation is not just a trend; it’s becoming a standard in efficient chiller operations.
Future Trends in Energy Efficiency
Looking ahead, energy efficiency will continue to be a driving force behind innovations in industrial chillers. With increasing regulatory pressures and consumer demand for sustainable practices, manufacturers are investing heavily in research aimed at creating even more efficient systems. Expect to see advancements such as variable speed drives (VSDs) becoming commonplace—allowing chillers to adjust their power usage based on real-time cooling needs.
Another emerging trend involves integrating renewable energy sources into chiller systems, reducing reliance on traditional power grids while cutting down on operational costs further. As companies search for reliable industrial chillers from reputable manufacturers like Carrier or York, they will increasingly prioritize energy-efficient models equipped with cutting-edge technology designed for long-term savings. The future looks promising as industries adapt to evolving standards in sustainability without compromising performance.
Conclusion

In wrapping up our exploration of industrial chillers, it's clear that these systems play a crucial role in various industries. From air-cooled to water-cooled options, understanding what are industrial chillers and their functions can help businesses optimize their cooling needs. Additionally, knowing what are the three types of chillers allows companies to choose the right equipment for their specific applications.
Overview of Chiller Types and Functions
Industrial chillers come in several types, each designed to meet different cooling requirements. The primary categories include air-cooled, water-cooled, and absorption chillers, each with its own advantages and ideal use cases. Understanding these distinctions is essential for anyone asking, What is a chiller vs HVAC? since both serve unique purposes in temperature control.
When looking at who makes industrial chillers, you'll find many manufacturers specializing in this technology. These companies focus on creating efficient systems that cater to diverse industries like food processing and chemical manufacturing. For those considering industrial chillers for sale, it's worth comparing prices from various industrial chillers manufacturers to find the best fit for your budget.
The Significance of Efficiency in Operations
Efficiency is paramount when it comes to operating industrial chillers; it directly impacts energy consumption and operational costs. Businesses seeking ways to reduce their carbon footprint should prioritize high-efficiency models that align with modern sustainability goals. Moreover, understanding how maintenance affects performance helps ensure that these systems operate at peak efficiency throughout their lifespan.
The price of industrial chillers often reflects their efficiency ratings; investing in more efficient models can lead to significant long-term savings on energy bills. Therefore, making informed decisions about which chiller system suits your operational needs can greatly enhance productivity while minimizing wasteful expenditures. Ultimately, embracing efficiency not only benefits the bottom line but also contributes positively to environmental stewardship.
Future Directions for Industrial Cooling Solutions
Looking ahead, the future of industrial cooling solutions lies in innovative technologies aimed at enhancing efficiency even further. Advances in refrigerant options promise better performance while reducing environmental impact—an essential consideration as regulations tighten around greenhouse gas emissions. Furthermore, smart controls and automation are paving the way for more intuitive operations that adapt dynamically to changing conditions.
As industries continue evolving towards greener practices and energy-efficient technologies become mainstream, we can expect exciting developments from leading industrial chiller manufacturers. Companies are also exploring hybrid systems that combine traditional refrigeration methods with cutting-edge alternatives like Arctic Active Cooling DC condensing units for enhanced flexibility and performance. In this rapidly changing landscape of cooling solutions, staying informed will be key to making wise investments in industrial chillers.