Introduction
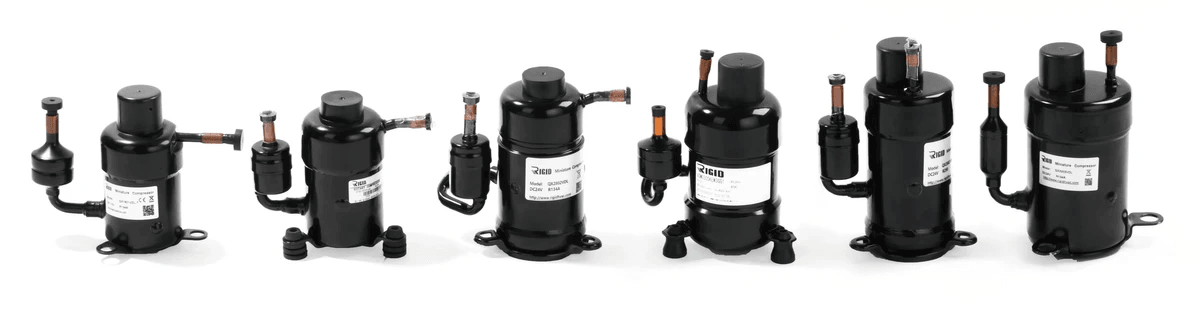
"Arctic Active Cooling. Endless Possibilities. We capture new technologies in mobile and compact cooling. Full-size cooling in a miniature design, customized to make your device stand out with innovative thermal management."
In the fast-paced world of technology, power electronics cooling has emerged as a critical component in ensuring the efficiency and longevity of electronic systems. As devices become more powerful and compact, effective cooling solutions are paramount to prevent overheating and maintain optimal performance. The evolution of power electronics cooling modules, particularly through innovations in liquid cooling solutions, is transforming how we manage heat in high-power applications.
The Importance of Power Electronics Cooling
The significance of power electronics cooling cannot be overstated; it directly impacts the reliability and efficiency of electronic devices. With increasing demand for higher performance in smaller packages, effective thermal management has become essential to avoid catastrophic failures. Power electronics coolers play a vital role in dissipating heat generated by high-power electronics, thereby safeguarding components from damage due to excessive temperatures.
Trends in Electronics Cooling Systems
Recent trends in electronics cooling systems highlight a shift towards more advanced and efficient methods to handle thermal challenges. Liquid cooling solutions are gaining traction as they offer superior heat transfer capabilities compared to traditional air-cooled systems. Additionally, the rise of passive and active cooling techniques showcases an industry-wide commitment to optimizing power electronics cooling for enhanced performance and energy efficiency.
Innovations in Liquid Cooling Solutions
Innovations in liquid cooling solutions have paved the way for groundbreaking advancements in power electronics modules. Technologies such as dielectric fluid cooling are now being utilized to provide safe and effective thermal management without compromising device integrity. As manufacturers continue to explore high-power electronics passive cooling methods, we can expect even greater improvements that will redefine standards for temperature management across various applications.
Understanding Power Electronics Cooling
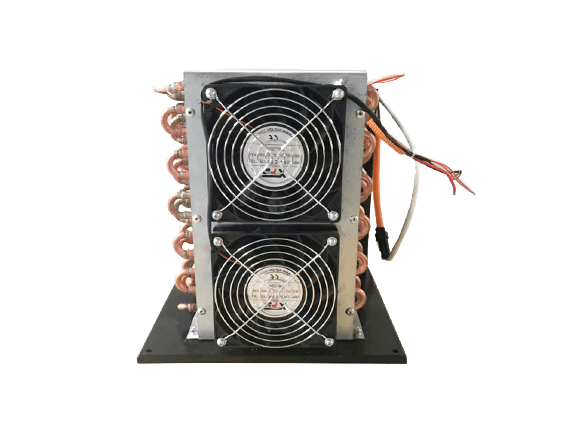
Power electronics cooling is a critical aspect of modern electronic systems, ensuring that devices operate efficiently and reliably under high power conditions. To achieve this, various cooling modules have been developed, each designed to meet the specific needs of power electronics applications. This section delves into the components and methodologies that define power electronics cooling.
What Are Power Electronics Cooling Modules?
Power electronics cooling modules are specialized systems designed to dissipate heat generated by high-power electronic devices. These modules utilize various techniques, including liquid and air cooling solutions, to maintain optimal operating temperatures within power electronics systems. By effectively managing thermal loads, these modules enhance the performance and longevity of electronic components, making them essential in industries such as automotive, aerospace, and renewable energy.
In essence, a Power Electronics Cooler incorporates advanced materials and designs tailored for efficient heat transfer. The integration of these cooling modules into electronics cooling systems is crucial for preventing thermal runaway situations that could lead to equipment failure or reduced efficiency. As technology evolves, so do these modules—adapting to increasingly compact designs while maintaining high-performance standards.
The Role of Dielectric Fluid Cooling
Dielectric fluid cooling of power electronics modules plays a pivotal role in managing heat within high-power applications. This method utilizes non-conductive fluids that not only absorb heat effectively but also provide electrical insulation for sensitive components. By circulating dielectric fluids around the power electronics cooler's components, engineers can achieve superior thermal management compared to traditional air-cooled solutions.
The advantages of dielectric fluid include enhanced thermal conductivity and reduced risk of electrical short circuits—both critical factors in maintaining system integrity under heavy loads. Additionally, this type of liquid cooling solution allows for more compact designs since it can handle higher heat densities without requiring extensive space for airflow pathways typical in air-cooled systems. As industries push towards higher efficiency levels in their products, dielectric fluid cooling emerges as an attractive option for future-proofing power electronics designs.
Advantages of High-Power Electronics Passive Cooling
High-power electronics passive cooling offers several advantages over active methods such as fans or pumps that require additional energy input. One significant benefit is the reduction in mechanical failure points; passive systems rely on natural convection or conduction rather than moving parts which can wear out over time. This reliability translates into lower maintenance costs and longer lifespans for electronic devices.
Another key advantage lies in energy efficiency—passive cooling techniques do not consume electricity during operation unlike their active counterparts which may draw significant power from the system they support. This characteristic makes passive solutions particularly appealing in scenarios where sustainability is paramount or where battery life is a concern—such as electric vehicles or remote installations with limited access to power sources.
Moreover, high-power electronics passive cooling can be seamlessly integrated into existing designs without requiring major modifications to an OEM's product line-up. By leveraging innovative materials and design principles like large surface areas or phase change materials (PCMs), manufacturers can enhance their products' thermal performance while adhering to stringent size constraints often demanded by modern technology trends.
Types of Effective Cooling Solutions
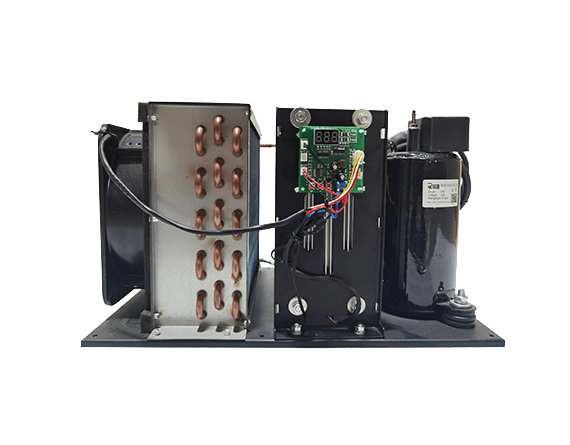
Cooling solutions for power electronics are essential for maintaining performance and reliability. With a variety of options available, it’s crucial to understand the differences and benefits of each type. This section will explore liquid cooling solutions, compare air-cooled and liquid-cooled systems, and delve into passive versus active cooling techniques.
Overview of Liquid Cooling Solutions
Liquid cooling solutions have emerged as a leading method for power electronics cooling due to their efficiency in heat dissipation. These systems utilize dielectric fluid cooling of power electronics modules, which helps to maintain optimal operating temperatures even under heavy loads. The ability to effectively manage thermal conditions is vital for high-power electronics applications, ensuring longevity and performance.
In liquid cooling systems, coolant flows through channels or tubes in direct contact with heat-generating components, absorbing heat before being cycled back to a radiator or chiller. This method significantly reduces thermal resistance compared to traditional air cooling methods, allowing for more compact designs in power electronics modules. As technology progresses, innovations in liquid cooling solutions continue to enhance their effectiveness and integration into various electronic systems.
Moreover, the use of dielectric fluids ensures that there is no risk of electrical shorts or damage to sensitive components during the cooling process. Liquid cooled systems can also handle higher thermal loads without compromising efficiency, making them ideal for modern high-power applications where space is at a premium. Hence, the adoption of liquid cooling solutions is rapidly increasing across industries relying on advanced power electronics.
Air Cooled vs Liquid Cooled Systems
When comparing air cooled vs liquid cooled systems for power electronics cooling, several factors come into play including efficiency, design complexity, and application requirements. Air cooled systems typically utilize fans or natural convection to dissipate heat; while they are simpler and less expensive upfront, they often struggle with higher thermal loads found in modern high-power applications. In contrast, liquid cooled systems excel at managing these demands by providing enhanced heat transfer capabilities through direct contact with coolant.
One significant advantage of using a Power Electronics Cooler that employs liquid cooling is its ability to maintain lower operating temperatures even under peak performance conditions. This not only prolongs the lifespan of critical components but also improves overall system reliability—an essential consideration when designing robust Electronics Cooling Systems for mission-critical applications. Furthermore, while air cooled designs may require larger footprints due to their reliance on airflow patterns and fan placement, liquid cooled configurations can be much more compact.
However, it’s important to note that integrating liquid-cooled systems can introduce additional complexities such as pump management and potential leakage risks; thus requiring careful engineering considerations during development stages. Ultimately choosing between air-cooled or liquid-cooled options should be based on specific application needs—balancing cost-effectiveness against performance requirements in the realm of Power Electronics Cooling.
Passive vs Active Cooling Techniques
The distinction between passive vs active cooling techniques plays a pivotal role in how effectively we manage temperature within power electronics modules. Passive techniques rely on natural mechanisms like convection or conduction without any moving parts; examples include heat sinks made from materials with high thermal conductivity designed specifically for high-power electronics passive cooling scenarios. While these methods can be effective under certain conditions—they often fall short when faced with extreme thermal challenges inherent in modern electronic devices.
On the other hand, active cooling techniques employ mechanical means such as fans or pumps that actively remove heat from components through forced circulation of air or liquids—this includes advanced strategies like dielectric fluid cooling used within sophisticated Power Electronics Cooling Modules today! Active methods provide superior temperature control which is crucial when dealing with fluctuating workloads typical across many industries utilizing cutting-edge technologies.
Choosing between these two approaches ultimately depends on factors such as space constraints within equipment designs along with anticipated thermal loads during operation periods; however blending both strategies often yields optimal results! By leveraging strengths from both passive & active methodologies—engineers can create highly efficient hybrid solutions tailored specifically towards unique application demands while ensuring reliable operation over extended lifetimes—a win-win situation indeed!
Impact of Temperature Management
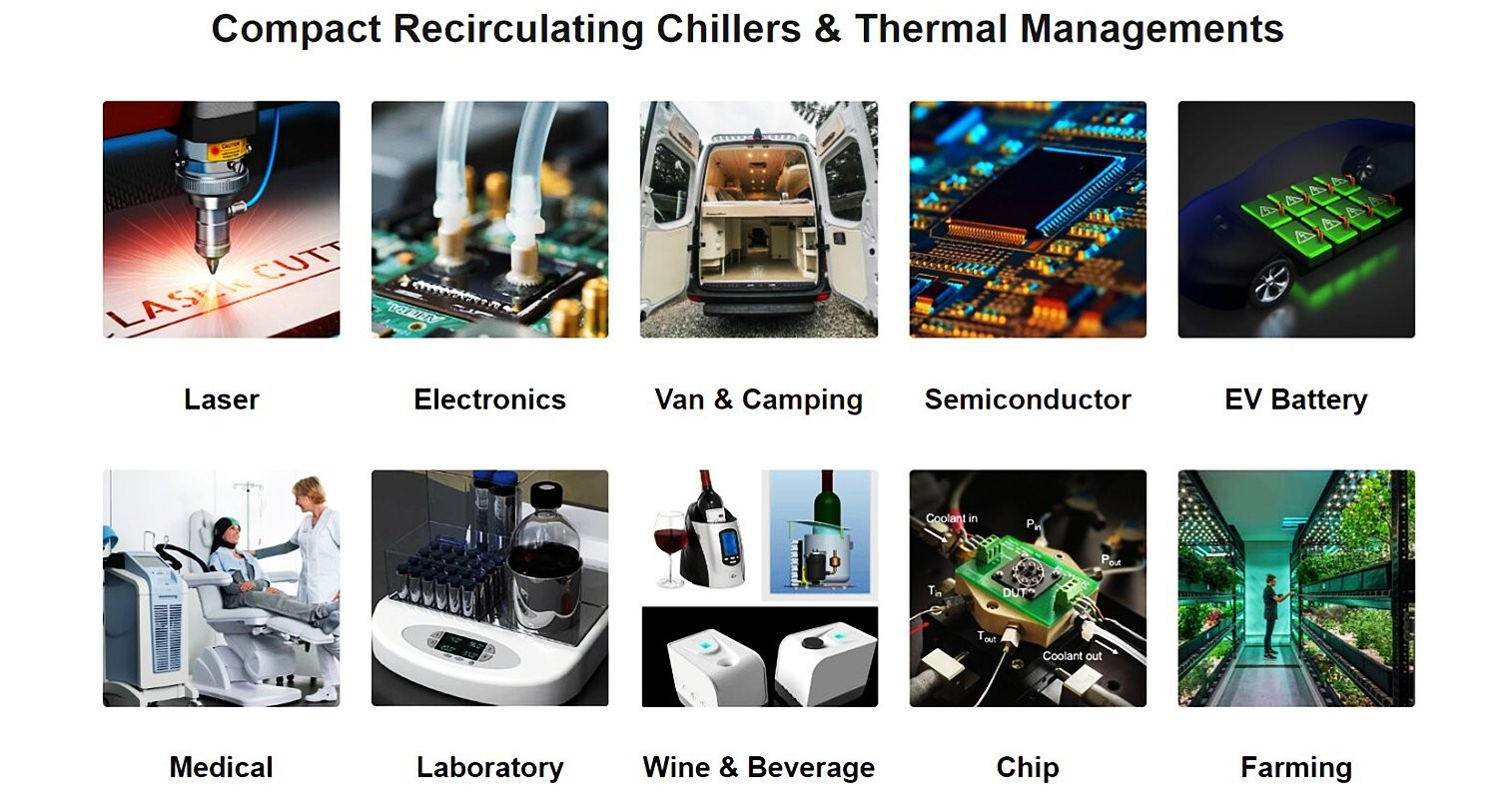
Temperature management is a critical aspect of power electronics cooling, influencing the efficiency and longevity of electronic systems. Effective thermal management ensures that Power Electronics Cooling Modules operate within optimal temperature ranges, minimizing the risk of overheating. As power density increases in today's electronics cooling systems, the need for reliable temperature control becomes even more paramount.
Thermal Management Importance in Power Electronics
In the realm of power electronics cooling, thermal management is not just a luxury; it’s a necessity. The performance and reliability of high-power electronics are directly linked to how effectively heat is dissipated from components. With advancements in applications such as electric vehicles and renewable energy systems, efficient thermal management strategies are essential to ensure that Power Electronics Coolers maintain their performance under demanding conditions.
Effects of Overheating on Performance
Overheating can have catastrophic effects on the performance of power electronics modules, leading to reduced efficiency or complete failure. When temperatures exceed specified limits, semiconductor devices can degrade faster than expected, resulting in significant downtime and increased maintenance costs. Furthermore, excessive heat can compromise the integrity of materials used in Power Electronics Cooling Modules, leading to premature failures and costly replacements.
Case Studies in Thermal Failure
Several case studies highlight the devastating impact overheating can have on electronic systems when proper cooling solutions are not implemented. For instance, one study documented a failure in an electric vehicle's battery management system due to inadequate dielectric fluid cooling of power electronics modules; this resulted in significant operational disruptions and repair costs exceeding thousands of dollars. Another case focused on industrial equipment where insufficient liquid cooling solutions led to unexpected shutdowns during peak operations—ultimately affecting productivity and profitability.
Arctic Active Cooling Solutions
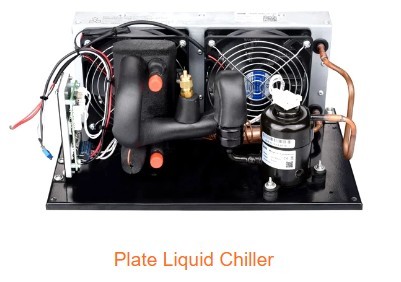
In the realm of power electronics cooling, Arctic Active Cooling has emerged as a leader with its innovative Coaxial Liquid Chiller. This high-performance unit is designed to meet the growing demands of modern Electronics Cooling Systems, ensuring efficient temperature management for high-power applications. By utilizing advanced technologies, Arctic Active Cooling delivers reliable and effective solutions tailored to the specific needs of power electronics cooling.
Features of the Coaxial Liquid Chiller
The Coaxial Liquid Chiller is a marvel in power electronics cooling technology, featuring a high-efficient refrigeration mini compressor that utilizes refrigerants like R134a or R290. Its compact design incorporates the smallest condenser and a coaxial tube evaporator, allowing for superior heat exchange efficiency in tight spaces where every millimeter counts. With additional components such as filter driers and drive boards seamlessly integrated into one unit, this system exemplifies sophistication and ease of use—perfect for those seeking advanced liquid cooling solutions.
Integration with Existing Systems
One of the standout aspects of Arctic Active Cooling's Coaxial Liquid Chiller is its ability to integrate effortlessly with existing systems. Power Electronics Cooler users can easily incorporate these cooling modules into their machinery or equipment without extensive modifications or downtime. The chiller's compatibility with customer control boards allows for direct connections to our BLDC compressor driver board, enabling precise control over compressor speed and optimizing performance based on real-time requirements.
Benefits for OEM and ODM Projects
For Original Equipment Manufacturers (OEM) and Original Design Manufacturers (ODM), Arctic Active Cooling's offerings present a wealth of advantages in power electronics cooling applications. By providing cutting-edge micro cooling solutions tailored specifically for customized projects, manufacturers can enhance their product lines while ensuring reliability and performance longevity in high-power environments. Moreover, our commitment to engineering excellence means that these customers receive not just products but strategic partnerships that foster innovation in Electronics Cooling Systems.
Future Trends in Electronics Cooling
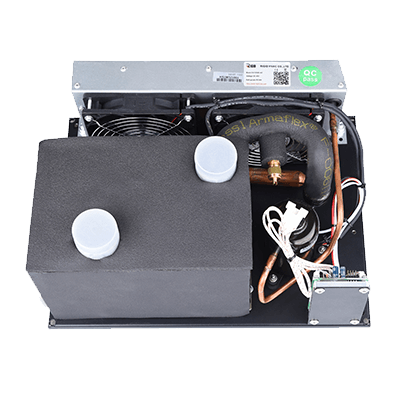
As the demand for high-performance electronics continues to grow, so does the need for advanced power electronics cooling solutions. Innovations in cooling technologies are paving the way for more efficient and effective methods to manage heat in power electronics modules. The future of electronics cooling systems lies in integrating next-generation technologies that not only enhance performance but also align with sustainability goals.
Next-Generation Cooling Technologies
Next-generation cooling technologies are revolutionizing how we approach power electronics cooling. With advancements in dielectric fluid cooling of power electronics modules, engineers can now design systems that dissipate heat more effectively while minimizing energy consumption. Liquid cooling solutions, such as those offered by Arctic Active Cooling's Coaxial Liquid Chiller, utilize sophisticated refrigeration components that allow for precise temperature control, ensuring optimal performance of high-power electronics passive cooling systems.
These innovative technologies are not just about better performance; they also focus on space efficiency and ease of integration into existing setups. The compact design of modern power electronics coolers means they can fit into tighter spaces without compromising on effectiveness or reliability. Furthermore, as industries seek to reduce their carbon footprint, these next-generation solutions promise a path toward greener operations while maintaining top-tier performance.
Eco-Friendly and Sustainable Cooling Options
In an era increasingly focused on sustainability, eco-friendly options for power electronics cooling are gaining traction. Manufacturers are exploring alternative refrigerants and materials that align with environmental standards while delivering efficient thermal management for power electronics modules. By incorporating sustainable practices into the development of liquid cooling solutions, companies can significantly reduce their ecological impact without sacrificing performance.
The demand for eco-friendly products is pushing the boundaries of innovation within the field of electronic cooling systems. From biodegradable materials to energy-efficient designs, every aspect is being scrutinized to promote sustainability in high-power applications. As a result, businesses embracing these eco-conscious strategies often find themselves ahead of regulatory requirements and consumer expectations alike.
The Role of Smart Technology in Cooling
Smart technology is becoming an integral part of modern power electronics cooling strategies, enhancing both efficiency and functionality within electronic systems. The incorporation of sensors and automated controls allows for real-time monitoring and adjustment of temperature management processes in power electronics cooler setups. This adaptability ensures that systems operate within optimal thermal ranges while reducing energy waste—a win-win scenario for manufacturers focusing on high-power applications.
Moreover, smart technology facilitates seamless integration with existing control boards used by OEMs and ODMs looking to optimize their machinery's performance further. By connecting Arctic Active Cooling’s Coaxial Liquid Chiller’s compressor driver board with customer control boards, users can fine-tune compressor speeds according to specific needs—maximizing efficiency while minimizing costs associated with overheating issues common in traditional setups. As smart technology continues to evolve, its role will only become more critical in shaping the future landscape of thermal management solutions.
Conclusion
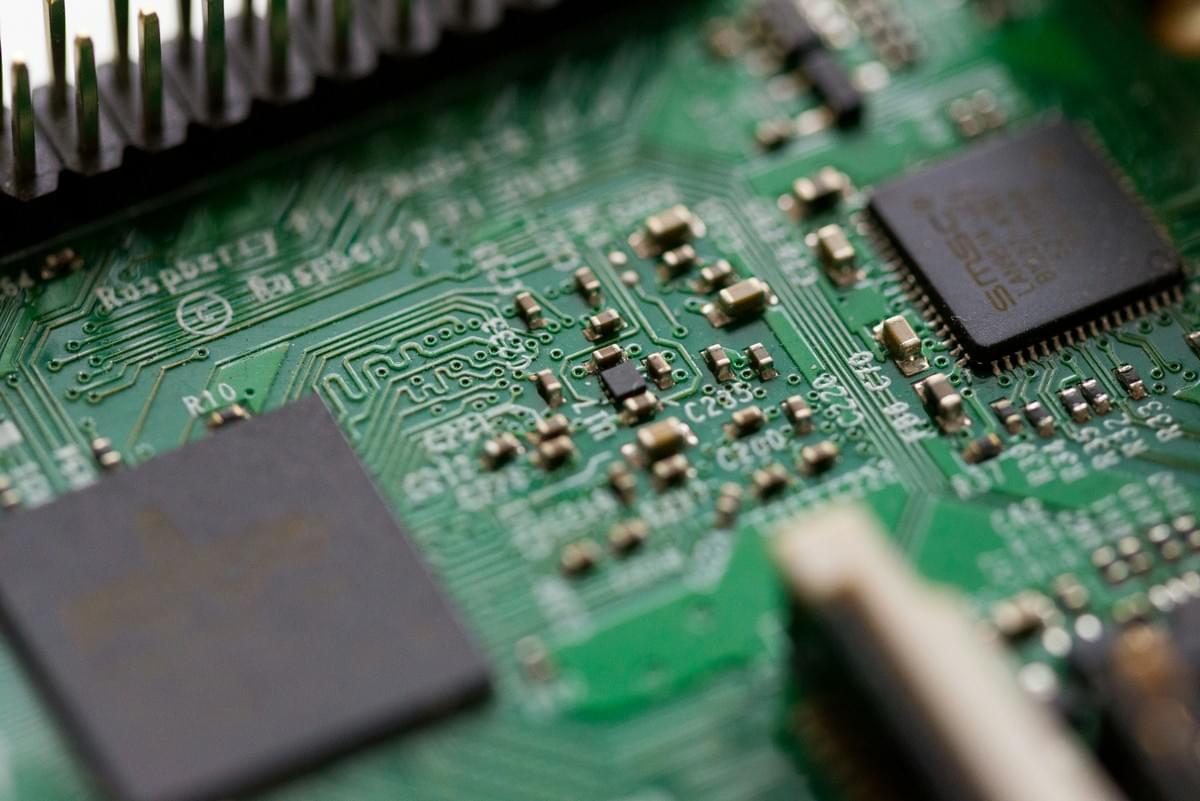
In the realm of power electronics cooling, the need for efficient thermal management is paramount. As electronic devices become more powerful and compact, effective cooling solutions are essential to maintain performance and reliability. The evolution of Power Electronics Cooling Modules has brought forth innovative strategies, including dielectric fluid cooling and advanced liquid cooling solutions that cater to high-power applications.
Key Takeaways on Power Electronics Cooling
Power electronics cooling is critical for ensuring optimal operation in high-performance environments. The integration of dielectric fluid cooling systems enhances the capability of Power Electronics Coolers by providing superior heat dissipation while minimizing the risk of overheating. Furthermore, understanding the differences between air-cooled and liquid-cooled systems can empower designers to choose the most effective solution for their specific power electronics needs.
Exploring Advanced Cooling Solutions
The development of cutting-edge liquid cooling solutions has transformed how we approach thermal management in power electronics. Innovations like Arctic Active Cooling's Coaxial Liquid Chiller exemplify this trend by offering compact yet efficient designs that integrate seamlessly into existing systems. These advanced Power Electronics Cooling Modules not only improve thermal performance but also enable manufacturers to customize their setups for optimal efficiency.
The Future of Thermal Management in Electronics
Looking ahead, the future of thermal management in electronics promises exciting advancements driven by smart technology and eco-friendly practices. Next-generation cooling technologies will likely focus on sustainability while enhancing performance through intelligent monitoring and control systems. As industries continue to evolve, embracing these innovations in power electronics cooling will be crucial for maintaining competitive advantage and ensuring long-term reliability.